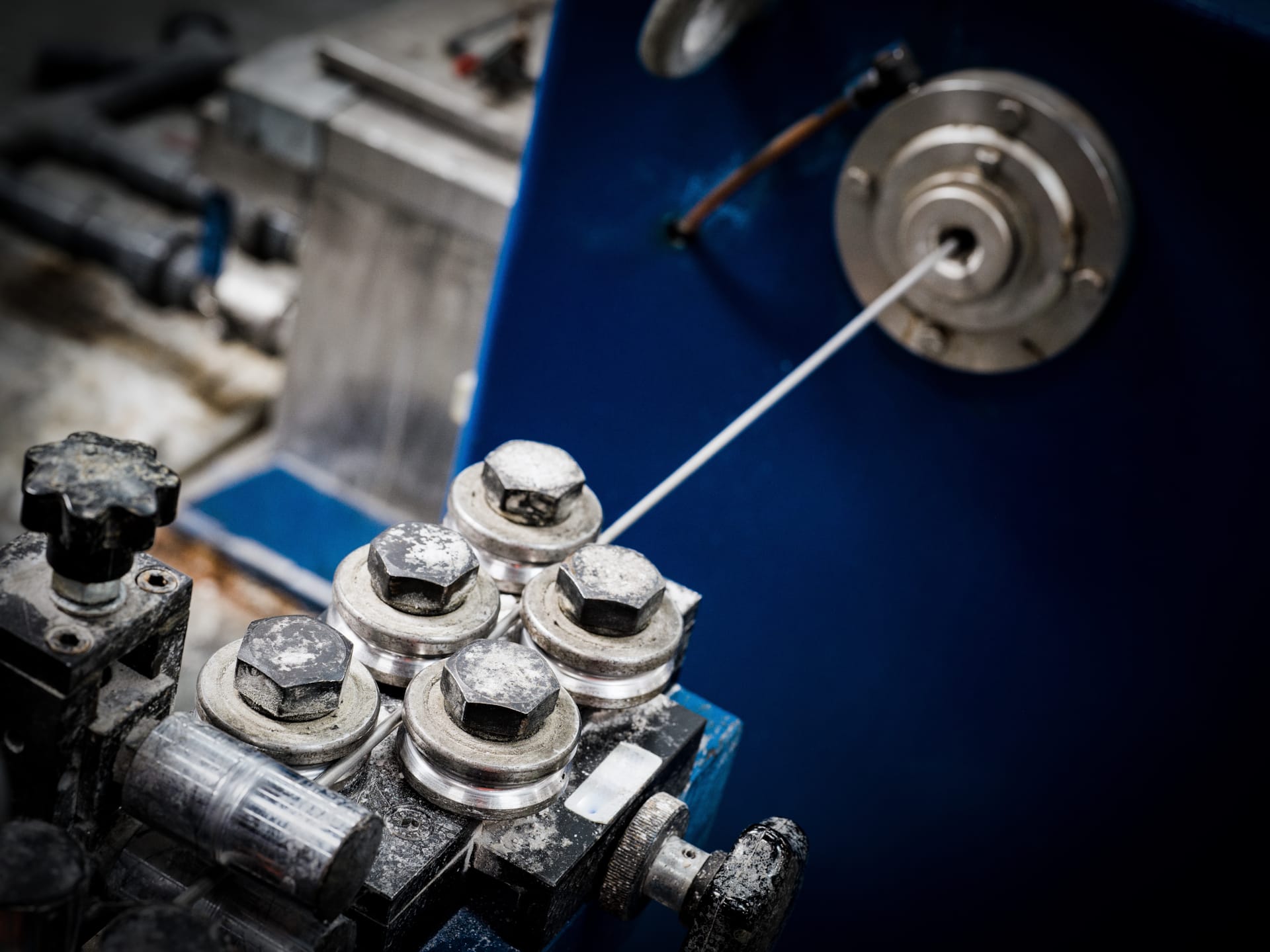
Tribology is the science of friction, wear and lubrication.
“Many aspects of our daily lives involve tribology,” explains Professor Mikael Olsson, showing us around one of Dalarna University’s laboratories in Borlänge, Sweden.
“When your shoe soles hit the ground, friction occurs. Materials wear against one another. This is an example of a tribological process. What Suzuki Garphyttan works with on a daily basis, drawing and shaping wire, is right at the heart of what tribology is needed for”. Mikael led a course at Suzuki Garphyttan over three, well-attended training events. These were attended not only by Research & Development (R&D) employees but also by production personnel. Olsson calls the Suzuki Garphyttan initiative unique, saying that the full course, with some 30 participants, is a better way of spreading knowledge, than the company sending a few employees on specific courses.
“It was fun, because there was a drive and interest in the room that you don’t always find in regular teaching,” says Professor Mikael Olsson.
Continuous development is key
Johan Norström is a senior metallurgist, and Tomas Berntsson is a development engineer at Suzuki Garphyttan. They were responsible for the training initiative. They have both worked with development issues for many years, in Suzuki Garphyttan and in other industries.
“But you never really finish topping up your knowledge,” says Johan, and Tomas agrees:
“In conceiving new kinds of wire for new customers, we must be particularly meticulous. That’s why tribology is important.” Johan Norström has himself studied under the professor earlier in life and has run into him again in various contexts. Getting in touch with Mikael seemed natural for various reasons.
“Over the years, our niche has been in products with extremely good fatigue properties. In many cases, new products also demand a similar focus on properties of wear. These are areas in which Mikael has extensive expertise,” says Johan. Tomas and Johan has previously been involved in courses on, for example, stainless steel and heat treatment. Demand for this initiative was unusually high, however.
“The ambition has been to identify themes where young new employees can learn completely new things, but themes that are also stimulating for those of us who’ve been around a while. We got it right on that score with tribology,” says Tomas.
From theory to practice
According to Professor Mikael Olsson, Suzuki Garphyttan is well-equipped to continue developing its knowledge on tribology.
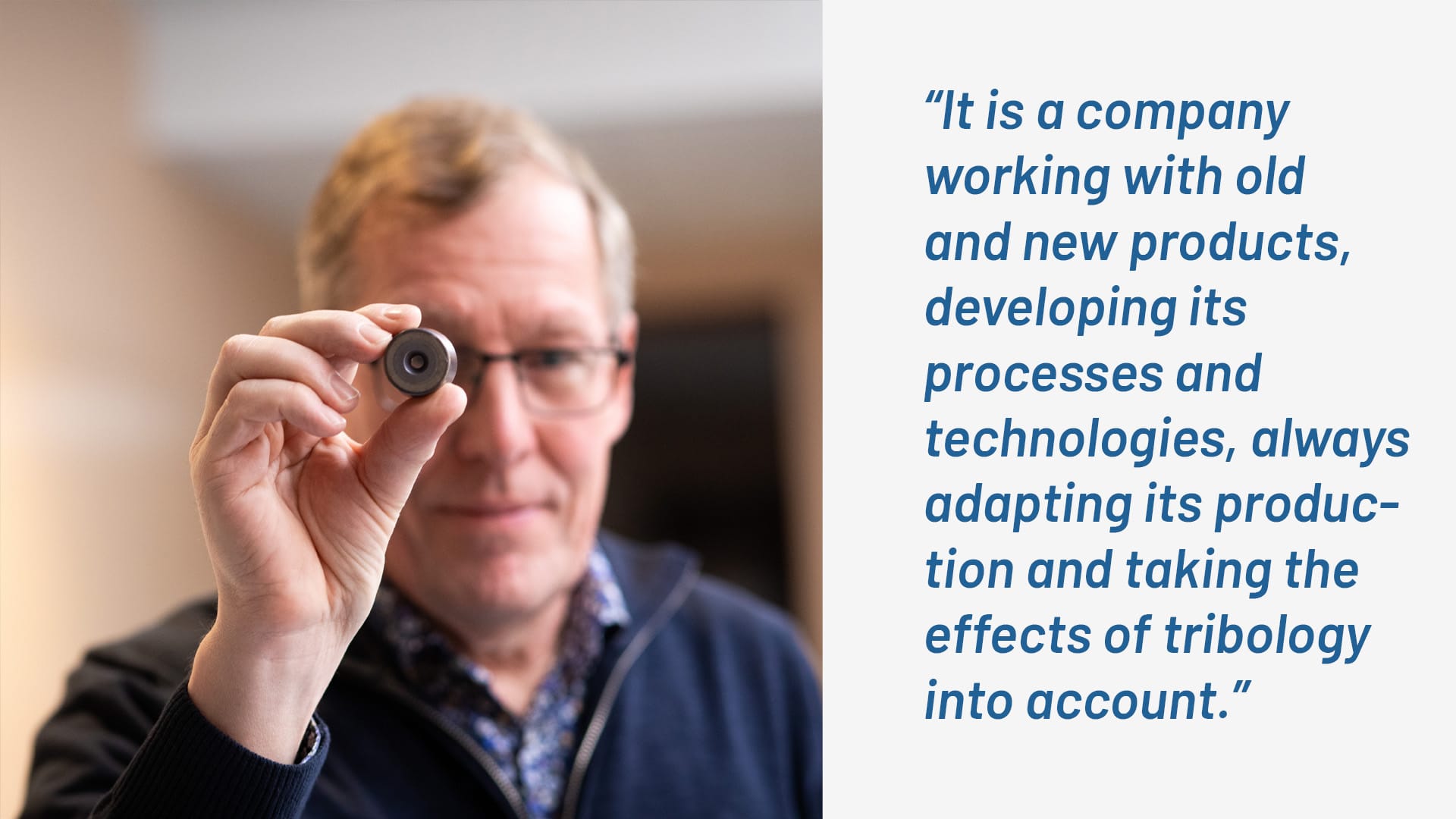
“It is a company working with old and new products, developing its processes and technologies, always adapting its production and taking into account the effects of tribology. I believe the considerable interest in the course reflects an urge to translate new knowledge into practice.” On one of his screens, the professor shows a highly magnified view of part of Suzuki Garphyttan’s production equipment. Pointing, he explains how only minimal adjustments to equipment and in speed and lubrication can have tribological effects potentially increasing efficiency and quality.
“The industries that take this knowledge in earnest are best equipped to meet their challenges best,” Mikael concludes.