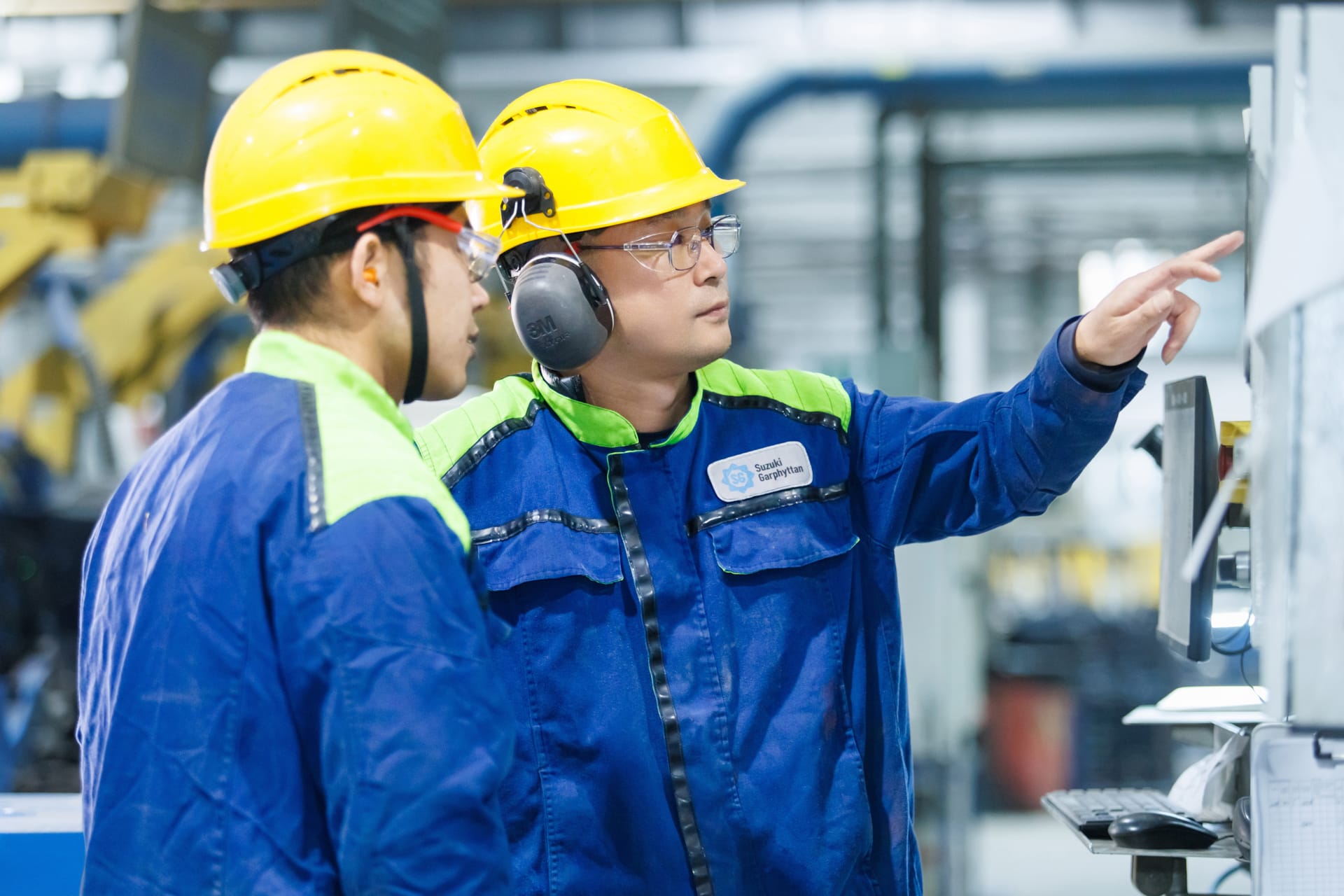
We have begun to phase out traditional hardening with oil and lead for more environmentally friendly alternatives. The first oil- and lead-free hardening line has been in operation for two years. A second line is being installed and will be in operation early in 2025. Significant efforts around the new technology have been made, both at the Research & Development (R&D) department in Sweden and on-site in Suzhou. The goal is to develop a hardening process that improves the working environment and reduces environmental impact, while maintaining the same superior quality that customers expect. The Site Manager in Suzhou, Erik Licht is pleased with the progress.
“Production capacity is in principle identical to using old technology. In some areas, we have greater flexibility. Quality-wise, we have used the upgrade to introduce several enhancements, including improved wire straightness and further reduction in hydrogen embrittlement.”
Improvements for employees
As Works Manager, Jacky has noticed positive changes along the production line:
“The investment entails using less oil and lead, which is positive in itself. But it also reduces the risk of fire. Overall, I see favorable effects on the working environment,” Jacky says. Erik agrees:
“The new hardening technology has been very well received by all employees. The improved working environment has been especially appreciated. Such a major change requires the involvement of many employees,” he says and continues:
“A key support measure in achieving successful implementation has been to address initial issues that surfaced as quickly as possible. It was certainly challenging, with some surprises and lessons learned. But it was also very rewarding to resolve key issues and start reaping the many benefits.”
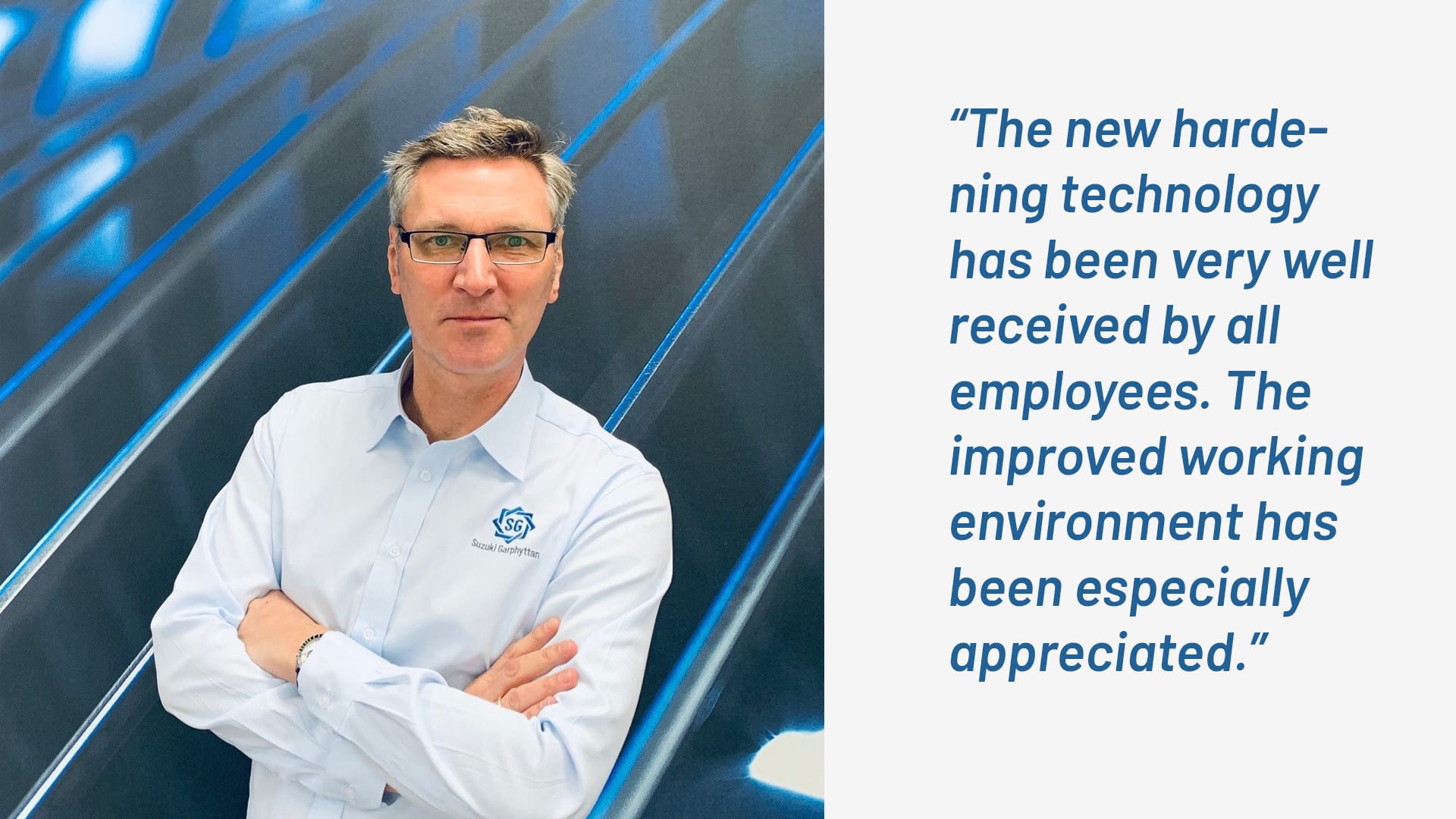
Continued development
For production employees, this was a good learning experience. According to Jacky, initial challenges have been tackled, and his team has a positive attitude towards new, more environmentally friendly machines.
“We will continue to lead the global wire industry now with this new, environmentally friendly hardening technology. Each coil's data can be controlled, monitored, and reviewed, enabling us to further enhance our wire quality.” Erik shares the same expectation and explains that the customers who have joined the transition to more environmentally friendly technology are satisfied.
“When important customers embrace new sustainable technology like this, it paves the way for broader adoption across the automotive industry. We are looking forward to soon having a second oil- and lead-free hardening line up and running.”