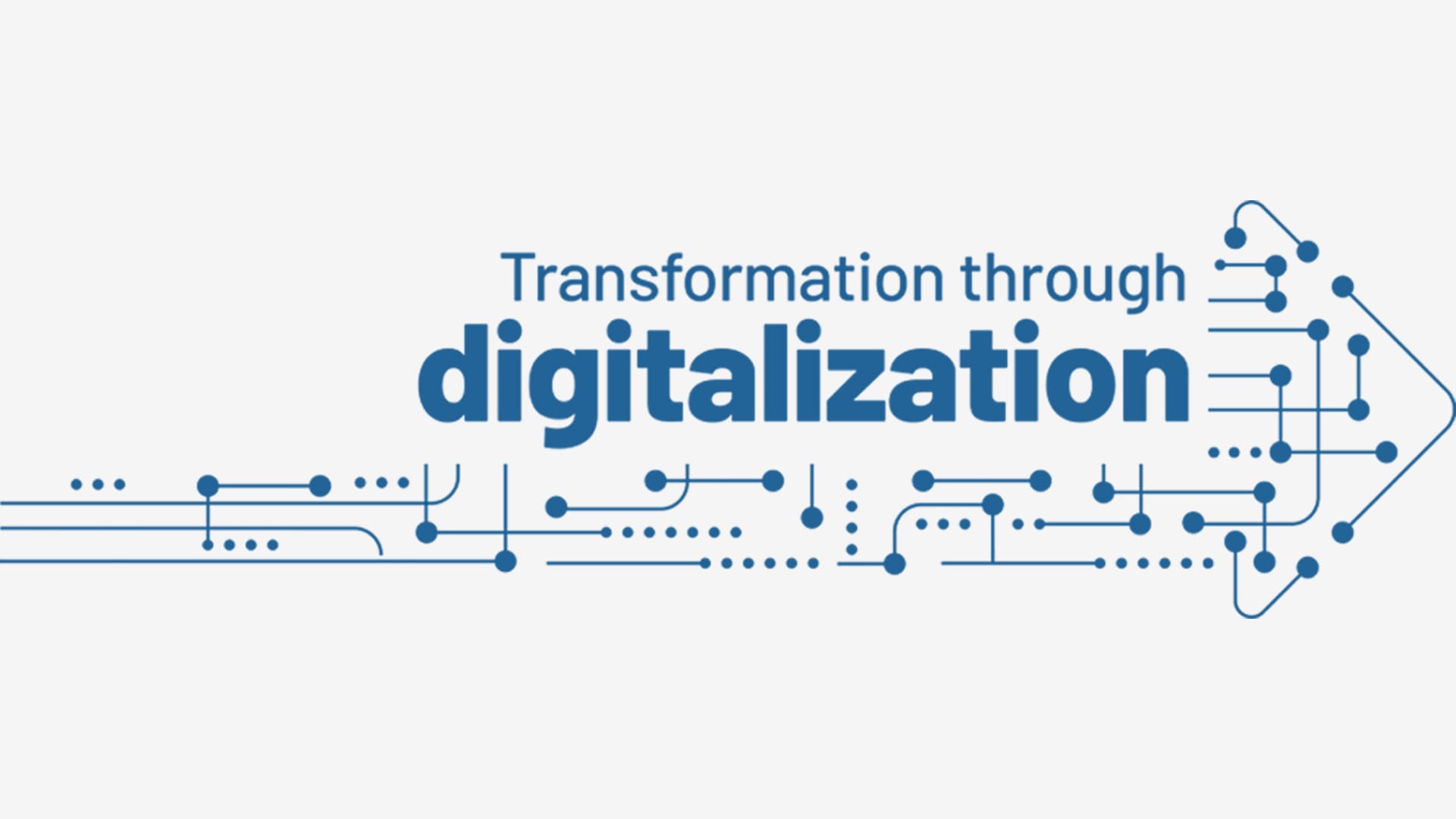
In 2024, Andreas Rendius, Digitalization Manager at Suzuki Garphyttan, saw the operations achieve considerable progress.
“Digitalization can contribute to so many good things. Product development, increased quality and smarter machine maintenance, to name but a few,” he says. Andreas describes his and his colleagues’ assignment as contributing to a knowledge cycle. Data gathered from the wire-production machines is put to better use when the opportunity for analyzing the materials increases, he explains. Both real-time data from sensors on the machines currently producing wire and older data gathered over the years should result in smarter decisions – improving conditions for greater customer satisfaction.
“With a data analysis platform from Microsoft, we can analyze data and learn a lot about what affects the quality of the wire and the wear on machines, for example. With time, conditions will allow real-time production-adjustment improvements when needed. This is a clear example of the many opportunities we are striving to capture,” says Andreas.
New technology provide opportunities
For engineer Nithin Santhosh Kanthaswamy, workdays are pervaded both by history and the future. Or, as he says:
“We who work here today stand on the shoulders of engineers whose work began many decades ago. However, the new technology provides us opportunities for refining the old methods.” His assignment includes finding ways to collect the best possible data from some of the first machines to be part of our digitalization ambitions.
“Since our production is complex, with multiple variables, such as speed, heat and lubrication influencing the end result, it is important to optimize sensors, placement and results processing alike”, says Nithin.
“From the raw material and the processes in the wire-drawing machines to what occurs in hardening, there is much to learn. We experience quite a few aha-experiences in this work, and I think we are pushing the envelope.”
According to Andreas, the team working with digitalization in production and the steering committees involved are ready to take the next step:
“Now that we are beginning to feel secure that the data collection and analysis are working, we will continue to work on a strategic plan. We face stimulating future development, which is important for Suzuki Garphyttan as the market is shifting rapidly. Interest exists among suppliers of both hardware and software involved in digitalization regarding our activities, which truly strengthens us in our ambition to continue.”
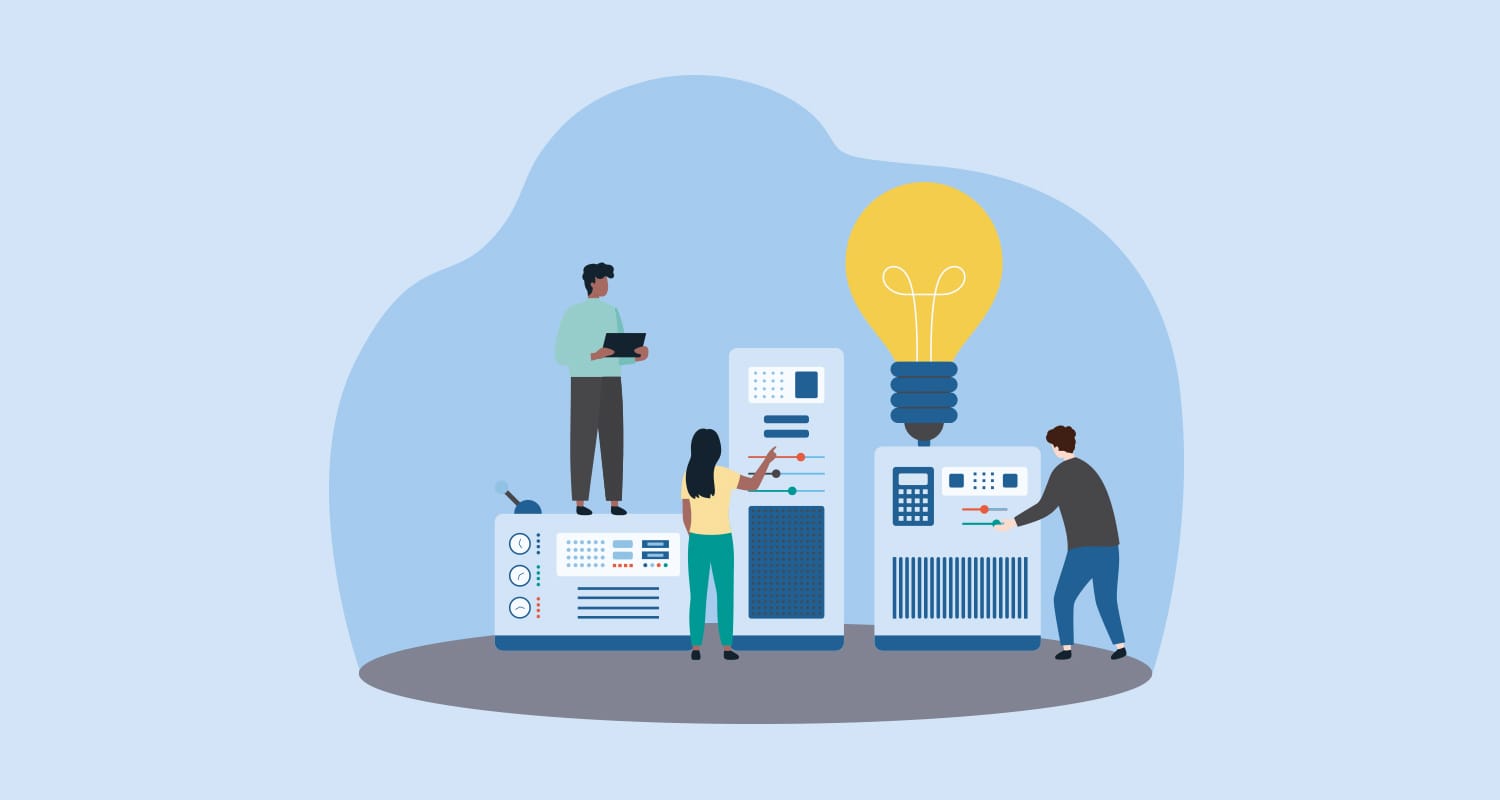