David Thureborn, Program Manager Automotive, reflects on this initiative:
“Our strategy to grow in volume and revenue, coupled with reducing dependency on components for combustion engines, led us to cold-drawn spring wire."
This decision, rooted in an extensive mapping of new automotive products back in 2020, aligns with the increasing demand for electric vehicles, ensuring Suzuki Garphyttan's continued relevance in an evolving industry.
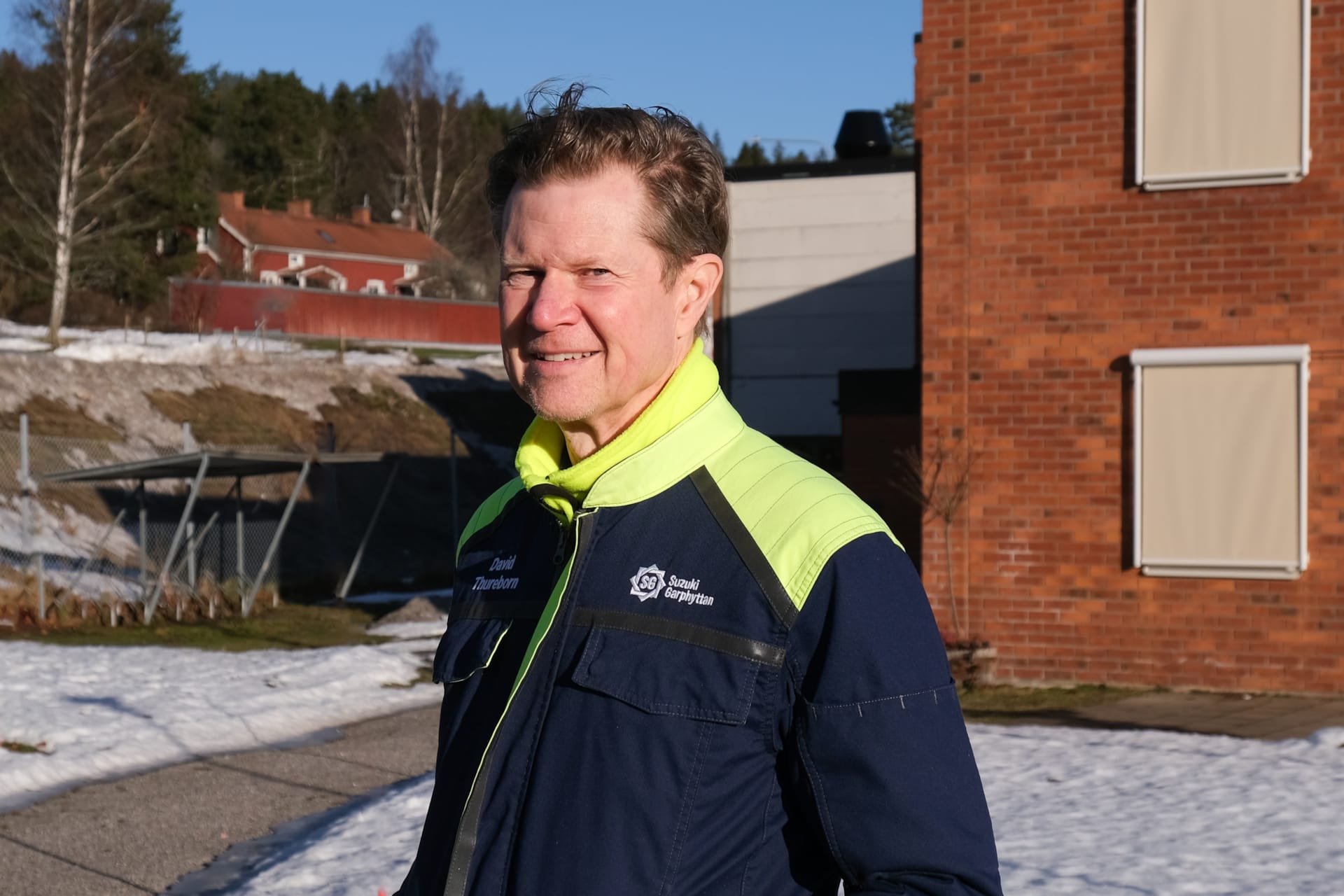
Development journey - from concept stage to product launch
The journey from concept to product launch for the cold-drawn wire has been thorough and strategic. David explains:
"We initiated a more targeted approach in 2022, involving mapping strategic customers and business opportunities, studying the manufacturing process, and more."
The global coordination and collaboration across Suzuki Garphyttan's various sites, including significant contributions from the teams in Suzhou and Garphyttan, have been crucial. This global effort, taking approximately nine months from project start to the first series delivery for Garphyttan, is a testament to the team’s determination and competence.
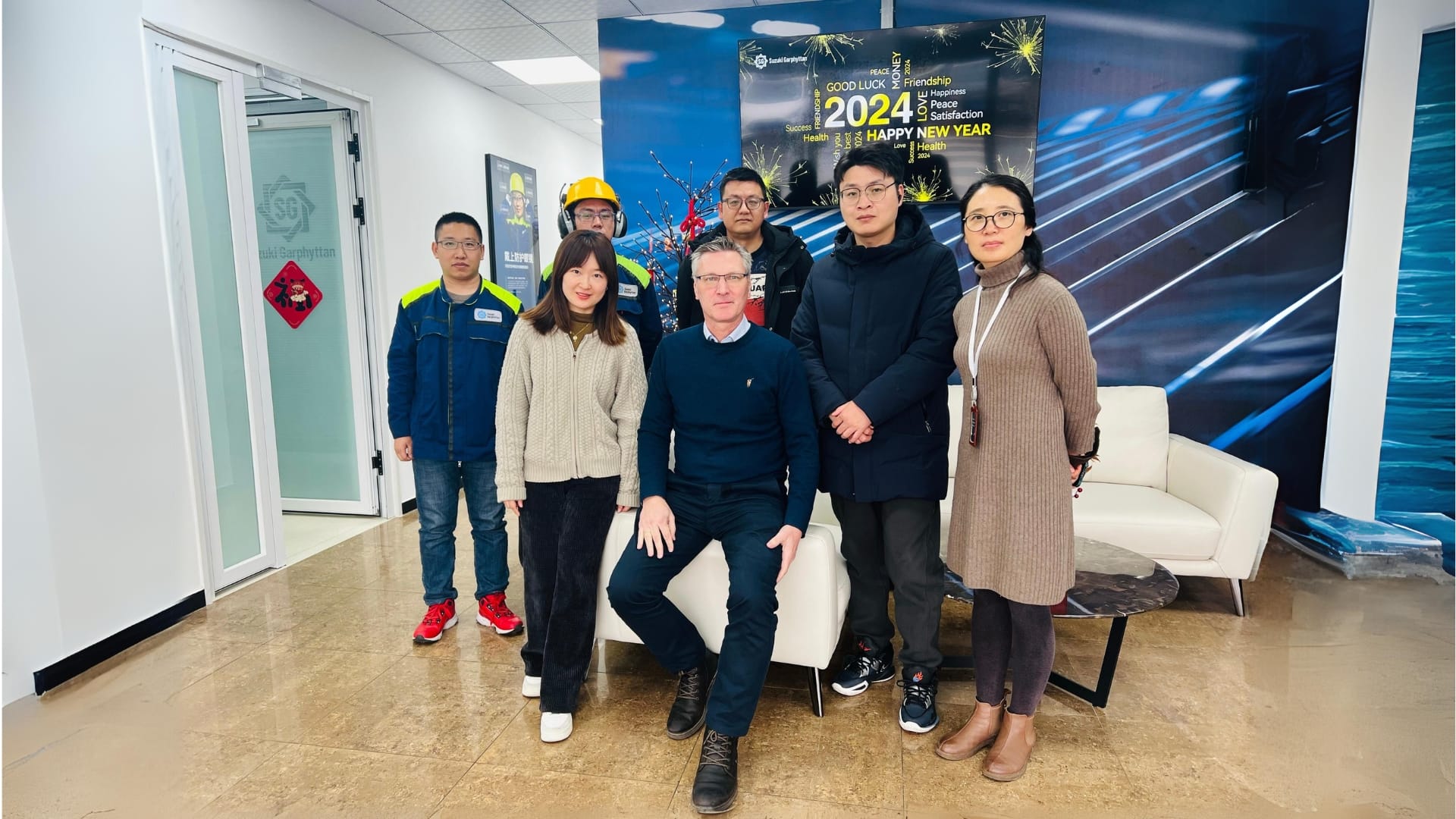
The tech behind piano wire and the market response
The cold-drawn spring wire, made from unalloyed carbon steel with a carbon content between 0.5 – 0.8 percent, is a high-strength material offered round as a standard, with rectangular and other shapes also available.
"The spring hardness is achieved through the drawing process. The more the diameter is reduced, the higher the hardness and strength. This process ensures high tensile strength and toughness, critical for the wire's diverse applications in everything from vibration dampers in machinery to springs in beds and furniture. The positive market response, especially the large number of springs meeting tolerance measures in our initial deliveries compared to our competitors, shows that our product is successful.”, David Thureborn explains.
Innovation and tradition
With the initial success, future plans for the product line are already in motion, focusing on expanding the range of dimensions and exploring further innovations. Reflecting on the project's challenges and rewards.
"The most fulfilling part has been working together to achieve a goal. Without the determination of several teams, we would not have completed the project on time", says David.
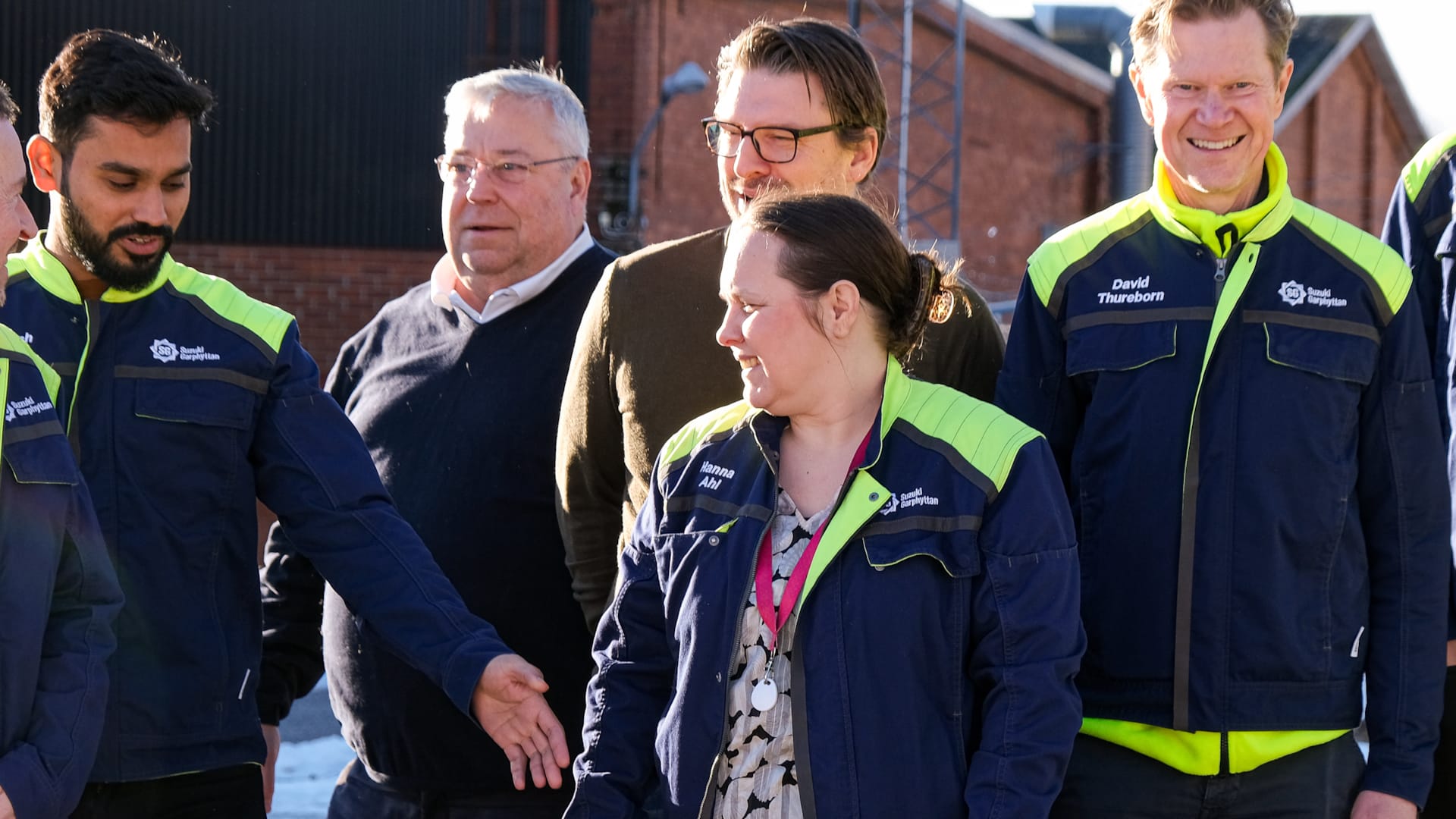
He also sheds light on the historical aspect of cold-drawn wire at Suzuki Garphyttan, tracing back to 1906 and into the 1980’s, which adds a layer of historical significance to this initiative.
“As we step into the future with this new wire range, we do so with a strategic vision and a nod to our rich heritage. This year has indeed been a leap forward, marking a new chapter in our history”, David concludes.