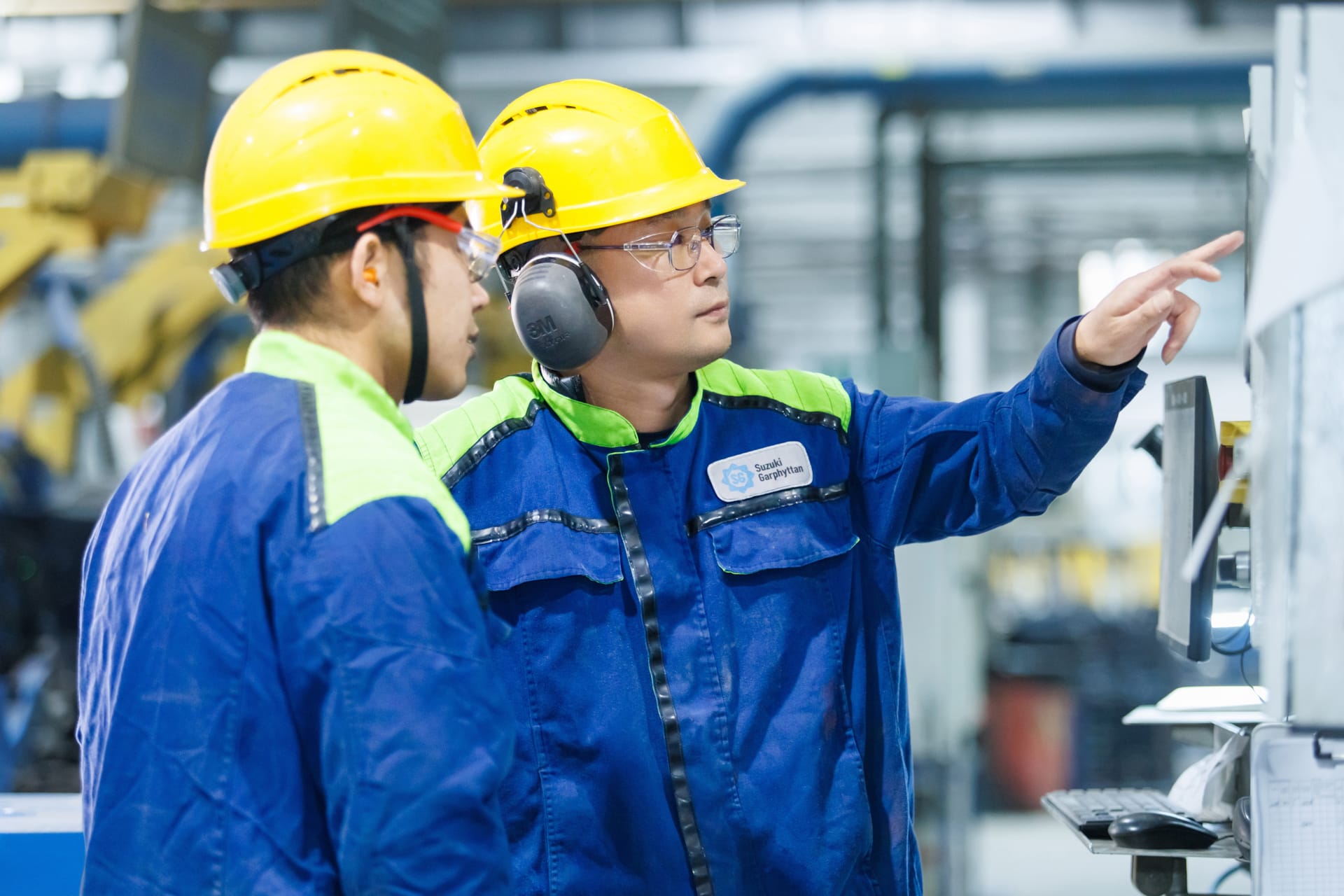
Hemos iniciado la eliminación gradual del temple tradicional a base de aceite y plomo en favor de alternativas más respetuosas con el medio ambiente. La primera línea de temple sin aceite ni plomo lleva operando dos años y se está instalando una segunda que entrará en funcionamiento a principios de 2025. Se han realizado significativos esfuerzos al respecto de la nueva tecnología, tanto en el Departamento de I+D en Suecia como in situ en Suzhou. El objetivo consiste en desarrollar un proceso de temple que optimice el entorno de trabajo y disminuya el impacto ambiental garantizando al mismo tiempo la calidad superior que se esperan los clientes.
El director del sitio de Suzhou, Erik Licht, se muestra satisfecho con el progreso efectuado.
“En principio, la capacidad de producción es idéntica que con el uso de la antigua tecnología. En algunas áreas, nos hemos dotado de una mayor flexibilidad. Desde el punto de vista de la calidad, hemos aprovechado esta actualización para introducir varias mejoras, como una rectitud superior del alambre y una mayor reducción de la fragilización por hidrógeno”.
Mejoras para los empleados
Jacky ha advertido cambios positivos en toda la línea de producción.
“La inversión implica no solo un menor uso de aceite y plomo, algo ya de por sí positivo, sino que también reduce el riesgo de incendio. En general, puedo observar efectos favorables en el entorno de trabajo”, afirma. Erik coincide:
“La nueva tecnología de temple ha obtenido una excelente acogida por todo el personal, siendo especialmente apreciada la mejora del entorno laboral. Un cambio tan importante requiere de la implicación de muchos empleados”, sentencia, para añadir luego:
“Una medida de apoyo clave para lograr el éxito en la aplicación ha sido abordar con la mayor premura posible las dificultades surgidas de inicio. Fue todo un reto, del que surgieron algunas sorpresas y lecciones aprendidas, pero resultó también muy gratificante resolver los principales problemas y empezar a cosechar los numerosos beneficios”.
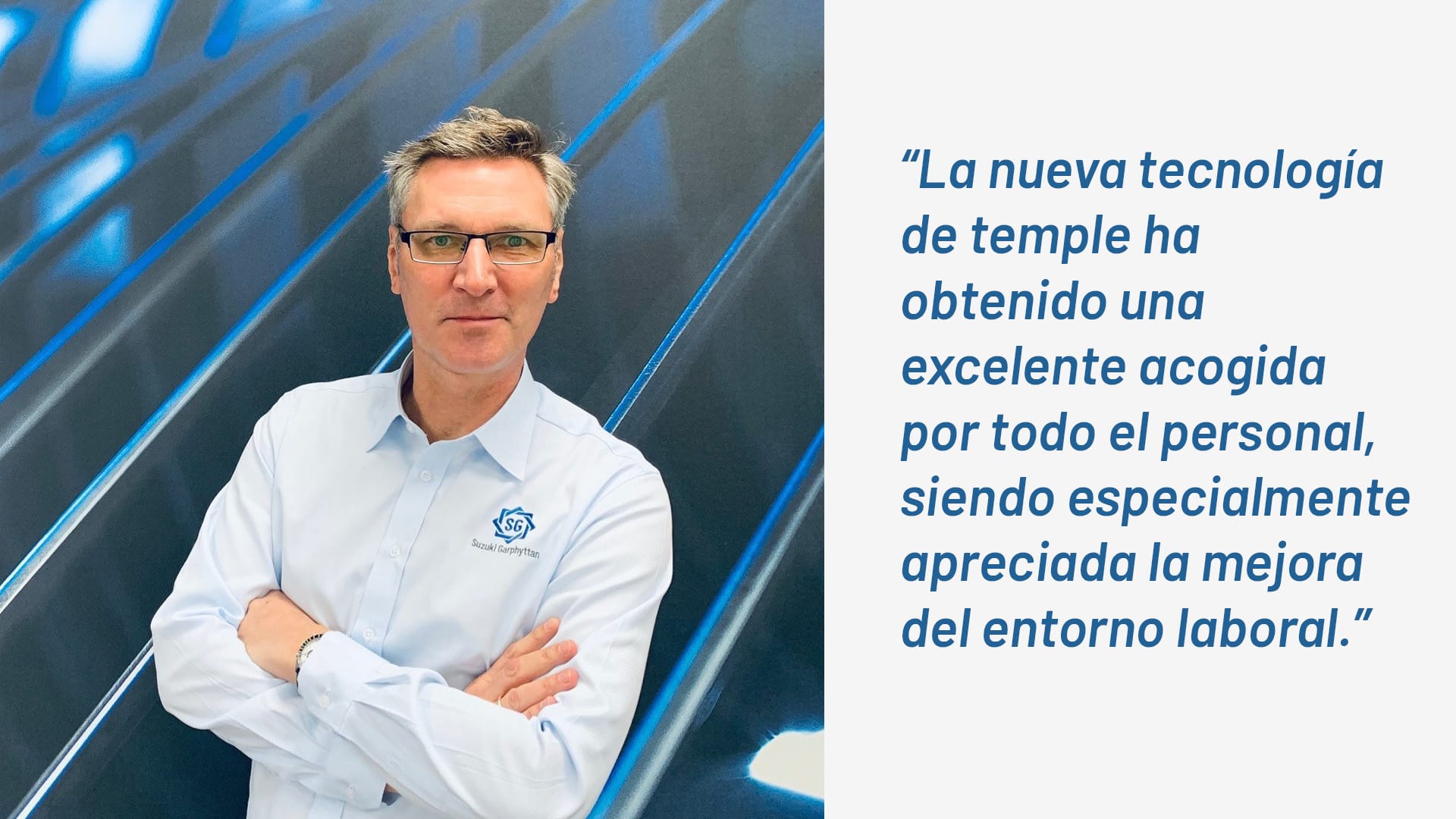
Desarrollo incesante
Para los empleados del área de producción ha constituido una enriquecedora experiencia de aprendizaje. De acuerdo con Jacky, se han solventado los desafíos iniciales y su equipo muestra una actitud positiva respecto a la nueva maquinaria, más respetuosa con el medio ambiente.
"Seguiremos ahora a la cabeza del sector global del alambre con esta nueva tecnología de temple ecológica. Los datos de cada bobina se pueden controlar, supervisar y revisar, lo que nos permite optimizar la calidad de nuestro alambre”.
Erik comparte dicha expectativa y alude a la satisfacción de los clientes que se han sumado a la transición hacia una tecnología más respetuosa con el medio ambiente.
“Cuando clientes importantes se adhieren a una nueva tecnología sostenible como esta se allana el camino para una adopción más amplia en el conjunto de la industria automotriz. Estamos deseando tener pronto en funcionamiento una segunda línea de temple sin aceite ni plomo”.