Element |
Weight % |
C |
0.09% |
Si |
0.70% |
Mn |
1.00% |
P max. |
0.040% |
S max. |
0.015% |
Cr |
16.00% - 18.00% |
Ni |
6.50% - 7.80% |
Al |
0.70% - 1.50% |
Cleanliness in steel
The presence of non-metallic inclusions in the wire rod is
inspected for every heat in accordance with the Suzuki
Garphyttan method by the steel supplier.
For wire rod samples: Inclusion size max. 15 µm down to 1 mm below surface. Inspection area: 350 mm2.
Inclusion size, surface |
5–10 |
> 10–15 |
>15 µm |
Max. number of inclusions |
Max grade D3 acc. to JK scale* |
20 |
0 |
* Method for assessment of the content of non-metallic inclusions. Swedish Standard SS 111116 – Microscopic methods – Jernkontoret’s inclusion chart II for the assessment of non-metallic inclusions.
Surface performance
AC-surface 0.30–5.60 mm Ø . The AC-coating can be removed before heat treatment by using a 10-20% nitric acid pickle at room temperature.
SURFACE CONDITION
Surface condition – non-destructive testing
In the standard size range 2.00-5,60 mm the wire can be tested continuously in Eddy Current equipment to a surface level of >40 microns.
Heat treatment
Normal procedure for precipitation hardening is heat treatment at 480oC (896oF) for 1 hour and then air cooling. This should be done as soon as possible after spring coiling. The tensile strength of the wire before and after this treatment is given in the table in previous page.
Shot peening
In order to obtain optimum fatigue properties, the process time should be adjusted to get a complete treatment. Size of shots should be adapted to wire dimension, pitch and shot peening equipment.
Shot peening of the inside of the spring coils is particularly critical.
Relaxation and fatigue properties
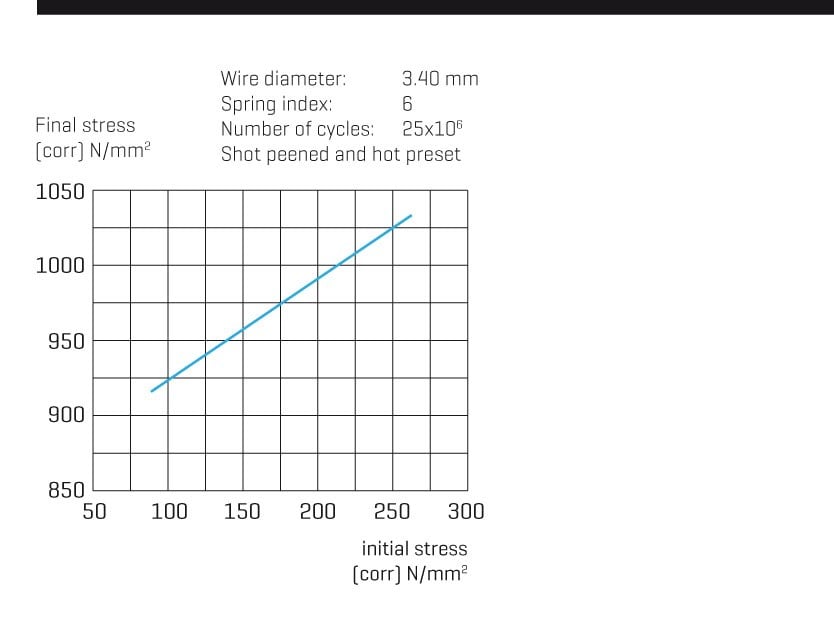
In diagram 1 the fatigue properties of GARBA 177 Supreme® is illustrated in a Goodman-diagram, based on a special test spring design.
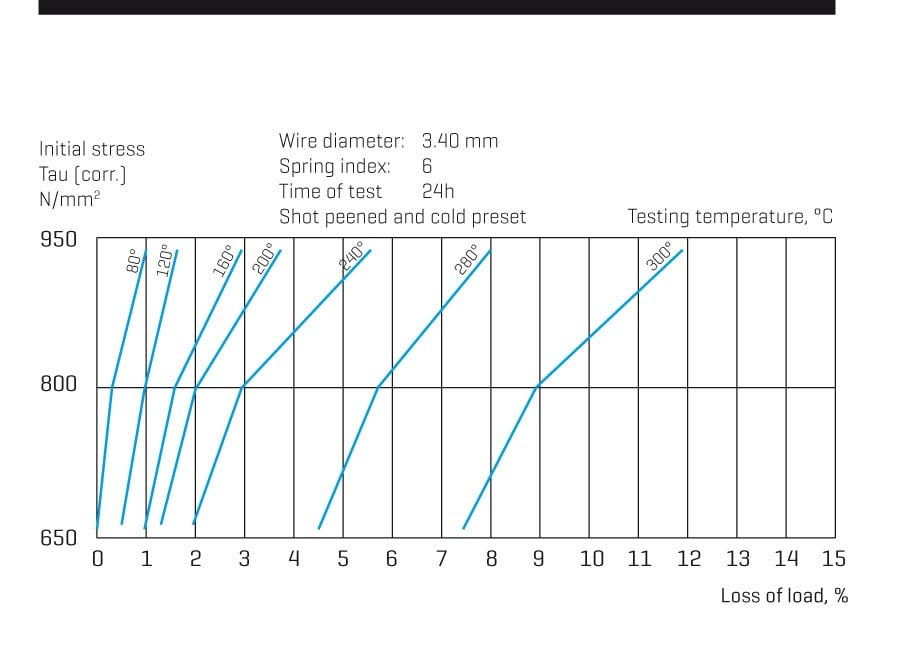
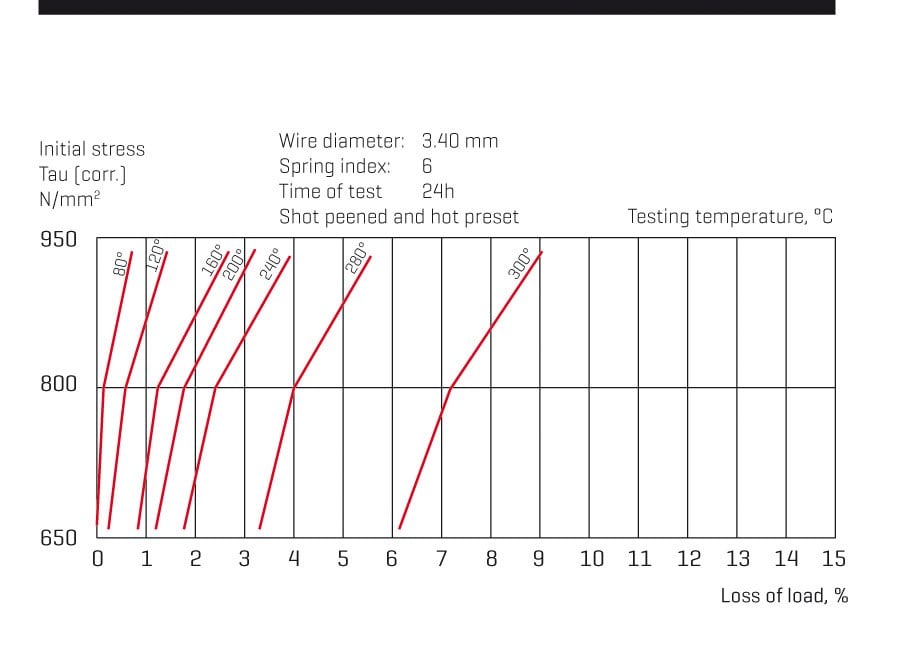
Diagram 2-3 show the relaxation properties (loss of load) of springs made from GARBA 177 Supreme® subjected to three different stress levels at different temperatures.